Scientists have created a very light foam using two-dimensional sheets of hexagonal-boron nitride (h-BN) that can absorb carbon dioxide.
The materials scientists discovered freeze-drying h-BN turned it into a macro-scale foam that disintegrates in liquids. But adding a bit of polyvinyl alcohol (PVA) into the mix transformed it into a far more robust and useful material.
The foam is highly porous and its properties can be tuned for use in air filters and as gas absorption materials, according to researchers.
The polyvinyl alcohol serves as a glue. Mixed into a solution with flakes of h-BN, it binds the junctions as the microscopic sheets arrange themselves into a lattice when freeze-dried. The one-step process is scalable, the researchers say.
“Even a very small amount of PVA works,” says Chandra Sekhar Tiwary, study coauthor and postdoctoral researcher at Rice University. “It helps make the foam stiff by gluing the interconnects between the h-BN sheets—and at the same time, it hardly changes the surface area at all.”
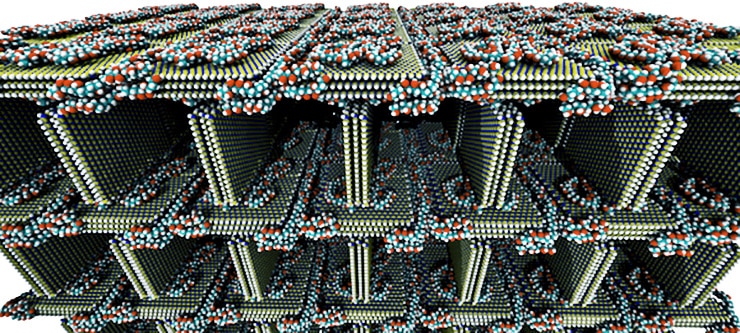
In molecular dynamics simulations, the foam adsorbed 340 percent of its own weight in carbon dioxide. The greenhouse gas can be evaporated out of the material, which can be reused repeatedly, Tiwary says. Compression tests showed the foam got stiffer through 2,000 cycles as well.
…the researchers want to gain control over the size of the material’s pores for specific applications, like separating oil from water.
And when coated with PDMS, another polymer, the foam becomes an effective shield from lasers that could be used in biomedical, electronics, and other applications, he says.
Ultimately, the researchers want to gain control over the size of the material’s pores for specific applications, like separating oil from water. Simulations carried out by coauthor Cristiano Woellner, a joint postdoctoral researcher at Rice and the State University of Campinas, Brazil, could serve as a guide for experimentalists.
“It’s important to join experiments and theoretical calculations to see the mechanical response of this composite,” Woellner says. “This way, experimentalists will see in advance how they can improve the system.”
Additional researchers contributing to the work are from Rice University; Chonbuk National University, Republic of Korea; Los Alamos National Laboratory; and the State University of Campinas.
Nanofibers turn mesh into see-through air filter
The Air Force Office of Scientific Research and its Multidisciplinary University Research Initiative funded the research.
The work appears in the journal ACS Nano.
Source: Rice University